Page name
What the logistics sector can learn from major changes in the Cold Chain industry

What the logistics sector can learn from major changes in the Cold Chain industry

Since 11 March 2020 when the World Health Organisation (WHO) declared a pandemic, we have seen drastic changes in the time taken globally to transport products and raw materials across all industries. New processes and practices have been implemented throughout to improve supply chain resilience.
Within Cold Chain in particular, the changes needed to be swift and precise as not only are these million-dollar shipments but they are also delivering life-saving medication and clinical trials in the fight against COVID-19.
The pandemic saw a rise in demand for cell and gene therapy shipments and immunotherapy-based medicines, with companies such as Marken doubling capacity in its Frankfurt facility (more than 40,000 sqft) and QuickSTAT doubling the size of its Belfast facility with more in-transit warehouses and conditioning facilities planned for development. Many companies took these precautionary steps to increase frozen room storage capabilities ahead of the greater impact of the pandemic and put greater focus on strategically placed regional and global networks of depots.
Another implication was the number of daily commercial flights, which are used to ship 70% of the medicines used in clinical trials. These flights were reduced to 10–15% of its pre-pandemic levels.
New Solutions
One business practice which became paramount to the Cold Chain industry’s success - to meet the increase in demand - was to implement Just in Time (JIT) business practices, a less wasteful distribution model formed in Japan. JIT is a ‘pull’ system of production, so actual orders provide a signal for when a product should be manufactured. Demand-pull enables a firm to produce only what is required, in the correct quantity and at the correct time.
Typically in pharma, the term JIT often triggers fear of ongoing shortages of comparator drugs and investigational medicinal products (IMPs). According to Frost and Sullivan, one third of global clinical trials were disrupted in 2020, affecting some $3 billion in new product revenue. Each day of delay to a clinical trial costs $37,000 and between $600,000-$8 million in lost opportunities. Research has shown that 85% of all clinical trials experience some kind of delay, 94% of them for a month or more.
With these figures in mind, it’s vital for Cold Chain companies to implement a JIT correctly and efficiently with minimal disruption, whilst maintaining service levels. To cater to this, some companies even booked chartered flights at a cost of over $100,000 each time to ship their medications for their client’s clinical trials. Pre-Covid Direct to Patient (DtP) trials would take several weeks to onboard, however this has been reduced significantly to just a few days.
One of the major benefits of implementing a JIT model is the flexibility to change materials, supplier or the overall desired outcome without the financial outlay of stocking ahead of time. Within the Cold Chain industry this comes with its own complexities. When dealing with clinical trials all elements including what packaging will be used; how the new drug is delivered; and how patients will take the treatment once they receive it - must be agreed ahead of time. A few years back, sponsors used to wait until they had the perfect protocol before starting a trial. Now they’ll start recruiting for a trial that they know will have to change and adapt throughout the clinical trial. In short, once agreement is in place for all parties, JIT principles can be applied to any operation from filling to labelling and kitting.
Changes adopted
Wider acceptance through requirement for DtP services eliminates a major problem with clinical trials - getting patients on site consistently, without attrition.
In America, DtP services have been widely accepted but even countries that were originally very resistant to the concept, such as Italy and Russia, changed its view in the wake of COVID-19. Out of 195 countries, the number of those permitting DtP shipments doubled to over 90 in 2020.
Since the pandemic, Marken (a specialist courier) was providing DtP services in 57 countries, this is now over 80 countries and with more to be added in the future. The COVID-19 surge has required strengthening and development of infrastructures in new countries.
For a risk-averse and often siloed industry, pharma made great progress in removing the barriers that can separate different stakeholders in clinical trials management and operation. For example, clinical operation used to be in one area and chemistry, manufacturing, and control in another. The clinical supply chain department functioned as the bridge to success. During the pandemic, vendors and sponsors are now functioning more as part of a unified group of stakeholders.
The pandemic created a ‘state of urgency’ in Cold Chain, expediting all aspects of the supply chain whilst meeting the rigorous regulation requirements to transport multi-million dollar shipments. With such large-scale changes being adopted with major benefits to the patients, pharmaceutical sponsors and the logistics providers, perhaps other areas of logistics with regulations to adhere too, such as Dangerous Goods ground transport in Europe (ADR), could see an overall increase to productivity by reviewing their aspects processes.
If you are working in sales or account management and you are seeking a role in the Cold Chain industry, please speak to me as I may have a role suitable for your background.
Contact us today
Spencer Riley’s team of highly dedicated, specialist consultants’ pride themselves on gaining a full understanding of our client’s business,
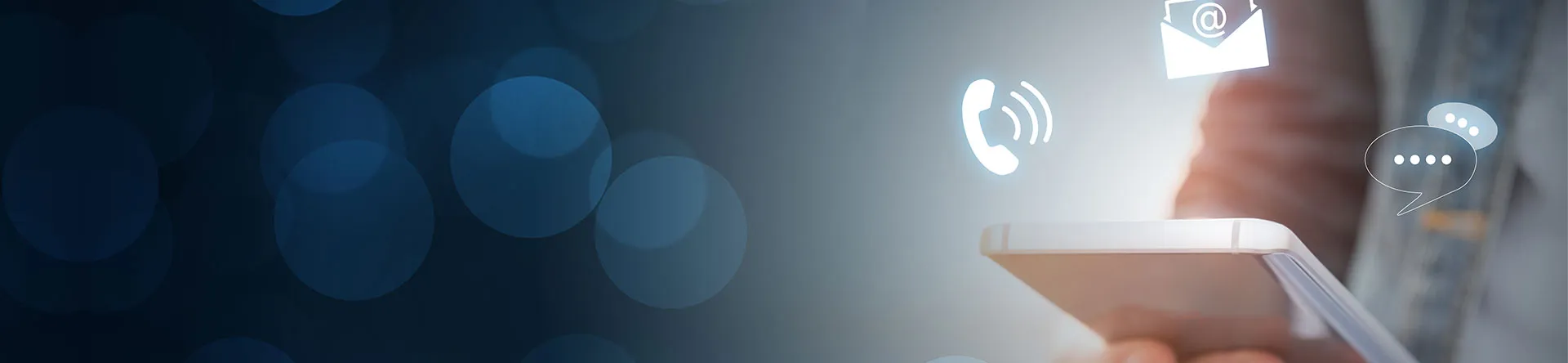